For the four major challenges of electric drive design for electric vehicles, TI introduces a real-time variable gate drive strength gate driver
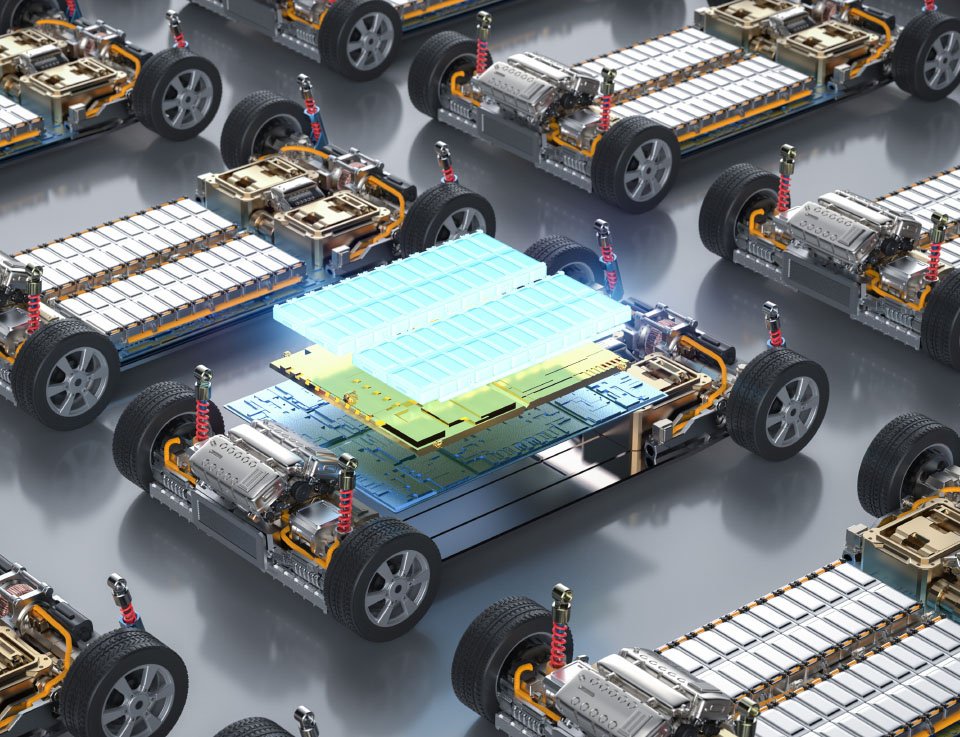
At present, there are four goals in the field of automotive semiconductor innovation: first, to help users extend the driving range of the car to a greater extent; Second, to help customers improve the charging performance and efficiency of electric vehicles; Third, through the innovation and change of semiconductor technology, make electric vehicles more affordable; Fourth, given that driving involves safety issues, customers need to be helped to make the design of electric vehicles safe and reliable.
On the other hand, in the design of high-voltage power supply and electric drive for electric vehicles, engineers also have four goals: first, hope to design a more efficient traction inverter; Second, it is necessary to increase the power density, reduce the volume under the same power output, or output more power under the same volume; Third, it is necessary to design a high-reliability system, because the traction inverter is related to power, safety and reliability are very important; Fourth, although the system requirements continue to improve, but from the design point of view still need to reduce the complexity of the system, so as to use fewer components to design the same function of the system.
To address these four challenges, Texas Instruments (TI) introduced the UCC5880-Q1 gate driver. Recently, at the launch of Texas Instruments UCC5880-Q1 SiC gate driver, Mark Ng, general manager of Texas Instruments Hybrid vehicle/electric vehicle department, said that using UCC5880-Q1's adjustable drive technology, designers can improve the overall efficiency of traction inverters according to working conditions; The high level of product integration also helps customers reduce design complexity and increase system power density. At the same time, TI's chips meet the functional safety ASIL-D design standard, so the reliability of the system can be greatly improved.
From a designer's point of view, traction inverters need to have more power, but also need to achieve safety, reliability and efficiency. On the market, the efficiency of traction inverter products has reached more than 90%, and it is difficult to continue to optimize, and the design needs of higher voltage and the use of new semiconductor devices will bring challenges such as product structure change and heat dissipation limitations. "After using our device optimization system, we estimate that the operating efficiency of the traction inverter can be improved by up to about 2%. Because the current product efficiency is already very high, the traction inverter high voltage module from IGBT to SiC will bring new challenges, so even a 2% improvement is a very high improvement in system design." Wu Wanbang stressed.
TI's overall strategy in the field of traction inverters is to provide total solutions for the system. The following chart shows the total solution TI can provide: In the entire traction inverter system, in addition to the isolated gate driver, it also includes ASIL-D MCU, C2000 real-time controller, fly-back controller (can act as the auxiliary power supply of the system), for future trends such as distributed auxiliary power, TI also has a fully integrated auxiliary power supply module, isolated voltage/current detection sampling, isolated power supply detection, etc.
In the case of the isolated gate driver UCC5880-Q1, he also stressed that TI not only provides a chip-level solution, but also a complete system solution. "We have a 300kW traction inverter reference design developed in collaboration with Wolfspeed, combining the UCC5880-Q1 with Wolfspeed's SiC module, and completing the overall testing and certification." "He added.
The UCC5880-Q1 drive increases the efficiency of the inverter system by up to 2% through lower system costs and real-time adjustment of the drive capacity, thereby extending the driving range of electric vehicles. For example, if the user charges three times a week, each charge can improve the driving range of 11km, over the course of a year can improve the driving range of about 1600km. In the UCC5880-Q1, TI designed the capability to adjust the grid drive strength in real time, allowing the user to adjust the drive current in the range of 5A to 20A while the system is running. Based on this, the device also complies with the ISO 26262 functional safety design standard, enabling designers to design traction inverter systems faster, safer and more efficient.
Why is adjustable drive important? "Silicon carbide can achieve higher switching speed, from the point of view of system efficiency, the faster the switching speed, the lower the switching loss, the higher the efficiency; From a system reliability perspective, faster switching speeds can lead to greater voltage overshoot, which can affect module reliability." He explained, "The adjustable drive feature we provide allows users to achieve a balance of switching speed and voltage overshoot, which is a performance advantage we bring to users."
In a discharge cycle, the battery works in a state of insufficient power for many times, at this time, it is difficult to reduce the switching loss and improve the efficiency. By adjusting the drive capacity of the system under different operating conditions, as well as the ability to switch on and off the current during each switching cycle, TI can help users achieve greater efficiency and system reliability. Specifically, in the fully charged state, such as more than 80%, the system is more concerned about the voltage overshoot can not be too high, at this time can be appropriate to reduce the drive capacity, so that the switching speed is slow, reduce the voltage overshoot. In the under-charged state, such as between 20% and 80%, the battery efficiency is very critical, and a large voltage overshoot can be properly allowed at this time, so the drive capacity can be improved.
A challenge also mentioned earlier is that customers need to achieve higher power density while achieving more power. "Therefore, in addition to the UCC5880-Q1 gate driver, we also used an isolated auxiliary power module, UCC14141-Q1, which is an integrated transformer isolated power module, can be used with UCC5880-Q1, very convenient design of distributed auxiliary power supply traction inverter drive bridge circuit," Helping customers achieve better functionality with smaller volumes and simpler circuits." "He added.
In the evaluation board, TI has designed the UCC5880-Q1 driver and the auxiliary power supply module UCC14141-Q1 together, and the number of components of the overall drive circuit is very small and the area is very small. Back to the previous mentioned that "TI not only provides chip solutions, but also provides overall solutions", the system in the following figure is the 800V/300kW silicon carbide traction inverter reference design designed by TI and Wolfspeed, a silicon carbide module supplier. This reference design not only includes schematics and PCB wiring, but also provides physical objects for customer evaluation. "Many functions of this system, including gate drive, auxiliary power supply, isolated power supply, MCU, are designed using TI's chip solution." "He added.
TI is also investing in high-voltage power technology. In electric vehicles, high-voltage technology will not only be used in traction inverters, but also in on-board chargers OBC and high-voltage to low-voltage DC/DC. The technology covers four main products: the first is gallium nitride, which is manufactured by TI in the car gauge grade. The gallium nitride solution provided is a fully integrated solution, whose drive, protection and power parts are all integrated in a single package, which can maximize the small size;
The second is the isolated gate driver, in addition to UCC5880-Q1, including other gate drivers also used in traction inverters, as well as high voltage gate drivers for OBC and DC/DC; The third is the auxiliary power supply scheme used together. TI can provide isolated auxiliary power module, which can achieve better performance with smaller volume; The fourth is the C2000 real-time controller, which can help customers design high-voltage power supplies more simply.
TI has three goals in the field of high voltage technology: First, through the innovation of semiconductor devices, to help users to minimize switching losses; Second, through small volume design, including simplified peripheral devices, to help users improve power density; Third, through technological innovation, the switching speed of the power tube is increased to a greater extent, and the driving strength is enhanced.
TI uses advanced high-voltage technology and chip technology innovation to help users design more efficient and reliable traction inverters, thereby extending the driving range of electric vehicles. The company aims to help users achieve the design goals of higher efficiency, higher reliability and higher safety through technological innovation, and at the same time reduce the cost of solutions through technological innovation, so that more consumers can buy more cost-effective electric vehicles, he concluded.
I prodotti a cui potresti essere interessato
![]() |
AMI-23-1-3 | LINE FILTER 250VAC 1A CHASS MNT | 8658 More on Order |
![]() |
AMI-29-1-3 | LINE FILTER 110/250VAC 1A CHAS | 8154 More on Order |
![]() |
AMI-29B-20-6 | LINE FILTER 110/250VAC 20A CHAS | 3960 More on Order |
![]() |
AMI-28A-10-1 | LINE FILTER 110/250VAC 10A CHAS | 3580 More on Order |
![]() |
AMI-27A-6-3 | LINE FILTER 250VAC 6A CHASS MNT | 4842 More on Order |
![]() |
AMI-M11O-1-20-B | LINE FILTER 250VAC 1A CHASS MNT | 8136 More on Order |
![]() |
AMI-21A-20-3 | LINE FILTER 250VAC 20A CHASS MNT | 4338 More on Order |
![]() |
AMI-M11P-1-10-B-1 | LINE FILTER 250VAC 1A CHASS MNT | 6480 More on Order |
![]() |
AMI-23B-12-3 | LINE FILTER 250VAC 12A CHASS MNT | 2394 More on Order |
![]() |
AMI-M12R-3-3-B-2 | LINE FILTER 250VAC 3A CHASS MNT | 6534 More on Order |
![]() |
AMI-M11K-7M-5-B-1 | LINE FILTER 250VAC 7A CHASS MNT | 6552 More on Order |
![]() |
AMI-22A-12-3 | LINE FILTER 250VAC 12A CHASS MNT | 4068 More on Order |
![]() |
AMI-22A-6-3 | LINE FILTER 250VAC 6A CHASS MNT | 8838 More on Order |
![]() |
AMI-M11VF-7-16-B | LINE FILTER 250VAC 7A CHASS MNT | 3906 More on Order |
![]() |
AMI-B11B-13-1-B | LINE FILTER 250VAC 1A CHASS MNT | 3508 More on Order |
![]() |
AMI-27B-10-1 | LINE FILTER 110/250VAC 10A CHASS | 6660 More on Order |
![]() |
AMI-29B-12-1 | LINE FILTER 110/250VAC 12A CHASS | 4986 More on Order |
![]() |
AMI-29A-8-1 | LINE FILTER 110/250VAC 8A CHAS | 5346 More on Order |
![]() |
AMI-27-1-1 | LINE FILTER 110/250VAC 1A CHAS | 5742 More on Order |
![]() |
AMI-29B-3-1 | LINE FILTER 110/250VAC 3A CHAS | 4698 More on Order |
![]() |
AMI-23-8-1 | LINE FILTER 250VAC 8A CHASS MNT | 7596 More on Order |
![]() |
AMI-M11A-1-20-D | LINE FILTER 250VAC 20A CHASS MNT | 2070 More on Order |
![]() |
AMI-21A-16-1 | LINE FILTER 250VAC 16A CHASS MNT | 4320 More on Order |
![]() |
AMI-M11J-3-1-B-1 | LINE FILTER 250VAC 1A CHASS MNT | 5976 More on Order |